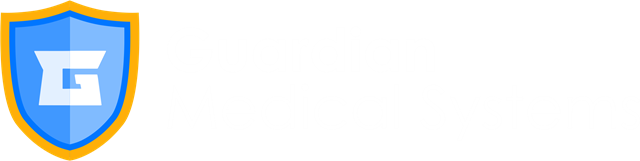
Choosing a USP Pharmacy Consultant
Why hire a USP consultant?
Many healthcare Project Leaders and Pharmacy Directors believe that once they have an architect and MEP group onboard, they are prepared for a successful pharmacy project design/build process. In the past, this probably was true. With the advent of USP 795, 797, and 800 this theory can result in multiple issues: substantial cost overruns, delayed inspection dates, and cleanrooms with constant pressure and temperature deficiency alarms or even indications of spore growth.
Large healthcare systems often use multiple architects and MEP groups who may not have experience with cleanrooms. New regulations or the desires of corporate pharmacy administration that often go beyond the stated regulations need to be taken into account. For example, many directors prefer 50-60 air changes per hour, as well as a separate air handler for their cleanroom space. This is far more than the 30 ACPH required by USP 800 and can increase the cost by $250,000 or negate a prospective location altogether. These considerations must be part of the budgeting process, which often occurs several years before the hiring of an architectural group.
Choosing the right consultant is not an easy task. While some consultants assist with only the design and equipment selection, others provide actual coordination of the supply, build, and installation process. The latter is what is referred to as a Turn-Key Consultant. These types of consultants ensure that the space, whether pharmacy or cleanroom, is operational prior to the various inspections required to open. This typically requires weekly meeting attendance and coordination with the general contractor (and their trade groups), as well as peripheral groups, such as network and IT personnel.
Prior to hiring, the Project Leader and Pharmacy Director should understand what allegiances the consultant has with the various equipment suppliers. There are consultants that on the surface seem devoted only to recommending equipment that meets the regulations and good practice. However, that same consultancy group might have taken money from equipment manufacturers for their endorsement. For this reason, the owner must understand where the various recommendations from their project team originate.
Choosing a consultant at the beginning may seem like an unnecessary expenditure, but the time and money a consultant can save over the course of a project can more than make up that cost. An experienced consultant will help guide you through the various pitfalls that can affect a project, smooth the coordination between the various trades, and help provide a finished project with minimal additional costs or delays.