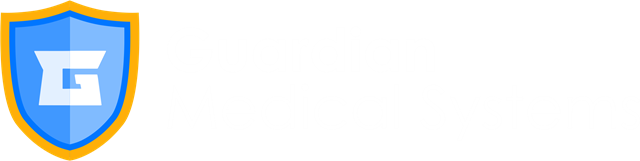
Cleanroom Pharmacy Manager Scheduling Requirements Prior to Opening
Scheduling for any cleanroom project can be a daunting task, especially in the final months. This blog is intended to provide an overview of some of the major milestones, including inspections and certifications, that will need to be completed prior to the cleanroom going live.
The Clinical Pharmacy Manager is usually responsible for scheduling many of the tasks listed below. Planning should occur at least two to three months in advance to allow for time to schedule inspections and coordinate with your General Contractor, Project Manager, and staff.
Cleanroom and Hood Certification Advanced Inspection
Open communication is essential among the Pharmacy Manager, Project Manager, and Cleanroom Certifier. The pharmacy manager should discuss the project scope with the certifier well before their scheduled meeting. In addition, the cleanroom plans should be provided and include the number and type of hoods, location, and layout. Also, consider providing the design for the HVAC system, as the Certifier may be able to point out any issues ahead of time. We recommend having the Certifier visit the project one to two weeks prior to the scheduled certification. These advance trips allow time to correct any issues that may be discovered. The terminal clean determines when the certification process can occur. Many factors can delay the certification process so open communication among the certifier and project manager is a must.
Refrigeration Logs
Refrigerators should be plugged in so that readings can be taken (either digitally or manually) to verify accurate operation. The BOP inspector may want to review 72 hours of daily readings. If taking manual readings, we suggest placing a log sheet on each refrigerator. If you plan on using an automated temperature monitoring system (installation lead-times can be up to 70 days) be sure that during the BOP inspection there is staff on hand familiar with generating a historical report.
HVAC Balancing
The HVAC balancing should be performed once the hoods have been installed and the construction and finish-work in the space is complete. Pressure Differential (PD) displays should be calibrated by the PD installer to reflect the Balance Technician’s airflow readings. This should be completed while the Balancer is onsite. During the Certifier’s visit, the Balancer should be present to change the airflow to/from the rooms and hoods in case an airflow adjustment is needed.
Terminal Clean
Hospital now completes a terminal clean. This should be scheduled especially if the hospital routinely uses an outside cleaning contractor. At this point, all traffic into the cleanroom spaces must follow cleanroom protocol without exception. This includes gowning protocols which must be followed for all who enter the space.
Cleanroom and Hood Certification Inspection
Once the terminal clean has taken place, the certifier will return and take samples, check airflow, etc. of the room and hoods. Lab processing of the samples can take up to 10 days. Should the samples indicate failure, the problem(s) must be identified and corrected, another terminal clean must be performed, and there will need to be another certifier visit. For this reason, scheduling the state inspection too close to the first certification attempt may prove problematic if you fail the initial certification/lab results. The BOP inspector will need a copy of the Certifier’s reports.
Board of Pharmacy (BOP) Inspection
The BOP will now inspect the spaces and interview pharmacy management. The refrigeration logs and certification papers should be current and available to the BOP inspector at the time of this inspection.
Department of Acute and Ambulatory Care (DAAC) Inspection
This is specific to pharmacies located in Pennsylvania. Generally, the DAAC inspection occurs after all other inspections but notification to the state of Pennsylvania must occur at least 60 days prior to opening. The notification requirements can be viewed here. It is strongly suggested to give the state notification well in advance of this deadline. Among the items to be provided during the inspection are equipment serial numbers, a list of equipment alarms, the alarm parameters, equipment warranty information, NIST certificates, etc. This information also serves the clinical staff far into the future for reference and warranty applications.
Note: The scope of this document is intended as an overview of some construction tasks requiring pharmacy management consideration/action, as well as common procedures often overlooked at the end of a build project. Not all considerations and inspections have been included. Chronological order is typical but may vary. Best efforts have been applied for accuracy; however, Guardian Medical assumes no responsibility for errors or omissions. Corrective comments are welcome and if necessary, will be applied to this blog once reviewed and verified. Please forward comments to info@guardianmed.net.