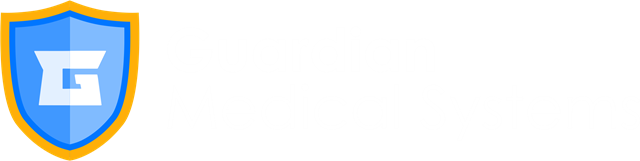
Keeping Your Cleanroom Clean
A Four Step System
There are four steps to USP <800> compliant cleaning procedures for Primary Engineering Controls: Deactivating, Decontaminating, Cleaning and Disinfecting. All areas and equipment where hazardous drugs (HDs) are handled must be deactivated, decontaminated and cleaned. Sterile compounding areas and devices must also be disinfected after these first three steps are completed.
Deactivation
The whole purpose of deactivation is to render the compound inert or inactive. This should be done using products that have known deactivation properties whenever possible. When selecting a deactivation product, care must be taken as some products may cause adverse effects such as respiratory effects, hazardous byproducts and caustic damage to surfaces. Damage is often exhibited by corrosion to stainless steel surfaces caused by sodium hypochlorite (if left untreated). In order to prevent this from happening, the sodium hypochlorite must be neutralized. For example, when using a 10 percent bleach solution, follow with a sterile distilled water rinse to remove any residue, and then with 70 % ethanol or similar non-corrosive antimicrobial agent for final decontamination.
Decontamination
In order to fully decontaminate, all HD residue from all non-disposable surfaces must be inactivated, neutralized or physically removed and transferred to absorbent materials appropriate to the area being cleaned. Some examples of appropriate absorbent materials are wipes, pads or towels.
When choosing a decontamination agent, make sure to choose an agent that has been proven effective for HD decontamination. This may include alcohol, peroxide, or sodium hypochlorite.
Make sure to check if your C-PEC has an area under the work tray that may gather contaminates because this will need to be deactivated, decontaminated and cleaned at least once a month to reduce contamination levels.
When Should Decontamination Occur?
- The work surface of the C-PEC must be decontaminated between compounding different hazardous drugs
- At least once daily (when being used)
- Any time there is a spill
- Before and after certification
- Every 30 minutes while compounding
- Any time voluntary interruption occurs
- If the ventilation tool is moved
- When surface contamination is suspected
Cleaning
After finishing with the decontamination process, the area should be cleaned with a germicidal detergent. Detergent selection is based on the type of soil to be removed as well as other cleaning mechanism factors.
After cleaning, use wipes or mops wet with sterile DIW or 70% isopropyl alcohol to remove all detergent residues from the surfaces.
Disinfection
When cleaning an area that is intended to be sterile the last step is disinfection. Follow the same procedures as for cleaning, except instead of using detergents, use liquid disinfecting agents. Disinfecting can be done using phenolic or quaternary ammonium compounds, but never both together. Occasionally, liquid sterilants such as peracetic acid, sodium hypochlorite, and hydrogen peroxide will be substituted for disinfectants but due to the corrosive nature of these sterilants, they should only be used intermittently.
Once disinfection is completed, disinfecting agent residues should be wiped from the surface with wipes or other cleaning tools that have been wet with sterile deionized water or sterile 70% IPA. This will eliminate the buildup of residue deposits that will cause staining of work surfaces.
In some cases, after completing all the previous steps, a PEC can be sterilized with a suitable sterilant such as vaporized hydrogen peroxide.
To Make a Long Story Short
When cleaning your cleanroom, make sure you are following the four step rule and always follow site and standard operating procedures (SOPs).
Sources
- USP Hazardous Drugs—Handling in Healthcare Settings
- Bureau Veritas North America, Inc-01/2014-C47014-000127 Cleaning Efficacy: Hazardous Drug Residues on 316 Stainless Steel
- ASU Biosafety Manual
- CDC/NIH Biosafety in Microbiological and Biomedical Laboratories (BMBL), 5th Edition, Appendix A – Primary Containment for Biohazards: Selection, Installation and Use of Biological Safety Cabinet.
- “Biological Safety Cabinets: Your 10 Step Decontamination Guide.” LabRepCo, LLC, 28 Mar. 2019, labrepco.com/2018/01/31/biological-safety-cabinets-10-step-decontamination-guide/.
- “Primary Engineering Controls.” Contec Healthcare, Contec Healthcare, contechealthcare.com/usp-797-guidelines/for-the-cleanroom/primary-engineering-controls/.
- Siegerman, Howard. “Cleaning Compounding Aseptic Isolators and Class II Biological Safety Cabinets.” Pharmacy Purchasing & Products, Sept. 2006.
- “Biosafety Cabinet Decontamination Guidelines.” Arizona State University, Apr. 2019.
- Depalma, A. (2019, September 1). Best Practice Tips for Biological Safety Cabinets. Retrieved January 27, 2020, from https://www.labmanager.com/product-focus/best-practice-tips-for-biological-safety-cabinets-817#.Ximmmc5KiUl